分类底漆,中涂,面漆型号8710-1 8710-2 8710-3固含量80%,99%包装规格25千克/组附着力1级使用方法辊涂刷涂平米用量0.3千克/平米执行标准GB/T5750-2006
供水管线内腐蚀介质种类较多,有酸、碱、盐、氧化剂及水蒸气等,涂料具有化学惰性、耐酸碱盐腐蚀,涂膜应结构致密,防水渗透性好,附着力强、坚韧丰满.
IPN8710系列涂料防腐操作工序少,能使防腐曾做到具有较好的均匀性和严密性能,IPN8710饮水防腐钢管尤其在防腐体变形处及焊缝处,也能做到涂料饱和,无布眼漏空后脆性起壳等现象。
目前,国内外食品容器内壁涂料大都选用IPN8710涂料,且采用底、面漆配套体系,该类涂料大都采用有机溶剂,随着环保法规的日益严格,溶剂型涂料的应用逐渐受到限制。
在食品容器的内壁涂上一层耐酸、耐油、耐碱的防腐蚀涂料,以饮用水或饮用品符合饮用卫生标准。
主要性能
(1)、无溶剂挥发,对环境友好,可直接与食品接触。
(2)平整光亮、坚硬、耐磨,物理机械性能好。
(3)耐水性能、耐化学品性能好。
(4)耐介质的防腐性能(耐酒精度高达50度、耐30%双氧水、耐10%NaCl)、耐高低温性能(耐低温可达-55℃、耐热可达80℃)等优于国内外同类产品的性能。
(5)可厚涂,一道干膜厚度可达200~1000μm,可单构成长效防腐涂层。
(6)底面漆合一,应用时无需底漆。
(7)涂料的施工适应性及其与基材的附着力好;可在环境温度为10~50℃的范围内施工,涂料与基材(钢铁基材)的附着力大于25MPa(拉开法)。
(8)涂料使用寿命长,正常使用寿命可达二十年。
施工条件:
施工环境温度宜为10~30℃,被涂装的基材表面温度应露点温度3℃以上,相对湿度应在85%以下。
基材处理:
(1)金属基材需喷砂除锈达到Sa2.5~3级,并用高压空气或吸尘器除净表面。
(2)非金属基材需清除表面粉尘、油污。

无溶剂环氧陶瓷涂料的组成无溶剂环氧涂料是采用低粘度环氧树脂、颜填料、助剂等经高速分散和研磨而制成漆料,以低粘度改性胺作为固化剂而组成的双组份反应固化型防腐涂料。
无溶剂环氧陶瓷涂料应用推广:
目前,我国石化工业发展正处于高峰期。从原油运输、储存中转、管道运输、炼油生产到成品油的储存,都需要建设大量储罐、铺设大量管道,这些储罐和管道如采用无溶剂环氧涂料,和传统的溶剂型防腐涂料相比,具有厚涂性好、防腐性佳、施工安全等优势,符合“、经济、环保、安全、节能”原则,具有十分广阔的应用前景。管道防腐埋地管道外壁常用防腐层有煤焦油瓷漆涂层、环氧煤沥青防腐涂料+玻璃纤维布复合涂层、3PE防腐层、熔结环氧防腐粉末涂层等,采用无溶剂环氧涂料的优势在于可现场施工、修补方便,无溶剂环氧涂料用于管道补口,施工十分方便快捷,但冬季低温时不便采用。根据不同腐蚀环境对防腐层的要求,将无溶剂环氧防腐层分为普通级和加强级,其中普通级干膜厚度≥400μm,加强级≥550μm。储罐内壁储罐内壁的防腐涂装通常都在安装完毕,试压结束,表面喷砂处理后进行,涂装环境比较密闭,自然通风条件很差,而采用不含VOC的无溶剂环氧涂料则可以降低通风量要求,消除爆炸危险。据杜邦公司宣传资料显示,其产品Permacor 2807HS/A灰色无溶剂热喷涂导静电环氧贮罐漆1981年用于德国北部某炼油厂5052号原油罐罐底板上表面和1米以下罐内壁,采用双进料加热喷涂设备喷涂一道,平均干膜厚度753μm,经21年使用后漆膜仍然完好,预计还可使用10年。
施工说明由于使用的无溶剂涂料是一种不含溶剂的环氧涂料,漆固体份含量高达98%以上,与溶剂型环氧涂料相比,在施工性能方面亦有一定差异,其大的差异在于粘度的增大与操作期的缩短。应注意采取以下措施:1、无溶剂环氧涂料选购时应注意所具备的施工条件,施工条件包括现场可行的施工方式(双进料热喷涂、单进料无气喷涂、辊刷等)和施工环境温度。通常在低于10℃时不适宜选用无溶剂环氧涂料;20℃以下时,建议选用冬用型无溶剂环氧涂料;20℃以上时,选用夏用型无溶剂型环氧涂料,这有利于获得适宜的操作期和涂膜干燥时间。2、涂料配制时考虑在使用期内的施工能力,在这段时间内能用完多少就配多少,以免配料太多来不及用而导致凝胶浪费。3、如采用单管进料的高压无空气喷涂方式施工,宜选用压力比大的无空气喷泵,适当的喷嘴管长度,提高总输出流体压力以顺利进料和雾化良好,选用合适口径和流量的喷嘴以能在操作期内用完所混合好的涂料。由于涂料甲乙组份分别进料,按比例在混合腔中混合后很快喷涂出去,这就解决了因无溶剂环氧漆预先混合后的操作使用期(Pot Life)太短而造成的施工难题。4、有些特别粘稠的无溶剂环氧漆,在小面积修补施工时,可采用刮涂的方式。
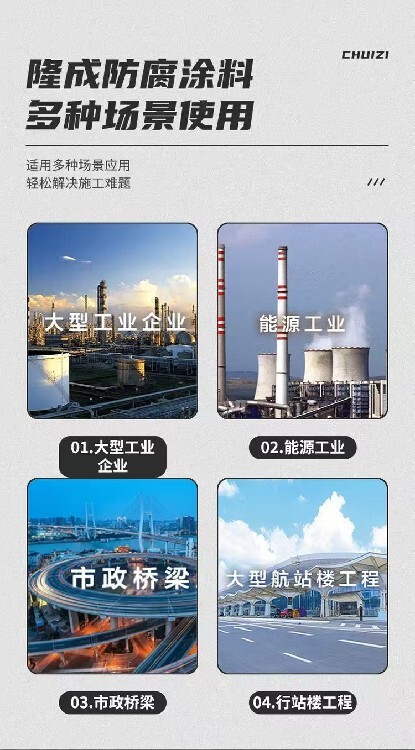
无溶剂环氧树脂底漆制作工艺主要包括:选择合适的原材料、确定配比和混合工艺、以及固化过程的控制等。这种底漆以其环保、耐腐蚀等特点,在工业涂装领域得到了广泛应用。以下是具体探讨:
1. 选择原材料
环氧树脂的选择:选择低分子量的液态环氧树脂,如E-44,有助于降低涂料的黏度,提高施工效率。
活性稀释剂的应用:使用甲苯基缩水醚、苯基缩水甘油醚、丁基缩水甘油醚等活性稀释剂调整黏度,其用量一般小于树脂质量的15%。
固化剂的选择:常用的固化剂包括多元胺和低分子量聚酰胺,根据实际需要选择合适的固化剂类型以适应不同的固化环境和要求。
2. 确定配比和混合工艺
组分比例的确定:按照一定的比例将环氧树脂与固化剂混合,确保两者充分反应,实现理想的涂层性能。
混合均匀性的要求:在混合过程中要确保两组分充分融合,避免局部配比不均影响涂层性能。
3. 固化过程的控制
常温固化与加速剂的使用:在常温下可进行固化,但为了提高固化速度,可适当加入加速剂,如苯酚、水杨酸等。
促进剂的应用:在低温条件下,加入适量的促进剂DMP-30可以提高固化效率,用量为聚酰胺的1%。
4. 施工方法的选择
设备施工:采用热喷涂或双口喷枪喷涂,确保涂料均匀涂布于基材表面。
配合比例与熟化:涂装前需按比例配合两组分,必要时进行熟化处理后施工。
5. 干燥与固化
常温干燥:一般情况下,采用常温干燥即可实现涂层的固化。
-烘干固化:对于绝缘材料的涂覆,可能需要通过烘干的方式来加速固化过程。
此外,在了解上述内容后,还需注意以下几点:
环保性:由于无溶剂环氧涂料几乎不含有机溶剂,VOC含量极低,因此更加绿色环保。
一次成膜厚度:无溶剂环氧涂料的一次成膜厚度可达200-300μm,提供了良好的防腐能力。
应用范围:适用于通风不良环境的设备涂装,如海上采油设备、装载石油的船舱、槽车、环氧地坪漆施工,是一种重要的重防腐涂料。
总的来说,无溶剂环氧树脂底漆制作工艺涉及了对原材料的精心选择、的配比和混合、固化过程的严格控制以及适宜的施工方法。这些特点使得无溶剂环氧树脂底漆在实际应用中展现出的性能,满足了现代工业对、环保涂料的需求。