激光波长 900-1100nm送粉方式同轴负压气载式送粉控制方式工控机+3轴控制系统卡盘与尾座之间载重>2T激光器半导体/光纤激光器主轴转速0-100r/min冷却方式 智能双温双控,20-40℃聚焦光斑圆形光斑、方形光斑卡盘直径500mm夹持长度3000mm激光功率6000-12000W
高速激光熔覆过程中影响加工的八大参数
1、激光功率:单位时间内激光器输出的能量。高速激光熔覆一般采用KW级激光器,如LT-3KW、LT-4KW等,市场应用广泛,能够满足大部分领域的需求。
2、光斑形状:光斑形状是影响熔覆质量的一个重要因素,光斑形状由激光器的光学系统决定。激光光束从送粉器射出后,经过扫描系统,再到基板上,在不同的位置形成不同的光斑。光斑形状直接影响着熔覆效果和成形质量。常见的光斑形状分为圆形和矩形两种,用户根据加工对象的特点选择使用。
3、光斑大小:光斑大小是指光束被扫描到基板表面的面积。激光熔覆过程中,激光能量聚集在熔覆层的中央,然后通过辐射向周围发散,光斑大小主要影响光功率密度,即单位面积的光能。相同功率条件下,光斑尺寸越小,光功率密度越大,高功率密度光斑适用于高包层。熔点金属粉末。
4、 加工距离:也叫搭接率,是指激光熔覆时,激光束从熔池中吸收热量所需的距离。激光熔覆过程中,光斑距离是影响熔覆质量的重要因素。在实际加工中,当光斑距离在3-5 mm范围内变化时,熔覆层质量良好,因此光斑距离一般控制在3-5 mm。
5、搭接率:搭接率是指熔覆金属粉末与基板的搭接率。搭接率是影响熔覆层表面粗糙度的一个重要参数。熔覆材料与基板之间的搭接率越大,越容易获得粗糙度较低的熔覆层表面。
光斑直径增大时,激光束能量密度提高,熔池受热变宽,熔化速度加快,在基板上产生较多的小孔。
搭接率提高,熔覆层表面粗糙度降低。但搭接部分的均匀性很难得到。每道熔覆层之间相互搭接区域的深度与每道熔覆层正中的深度有所不同,从而影响了整个熔覆层。高速熔覆的搭接率高达70%-80%(普通熔覆的搭接率为30%-50%)。
6、熔覆速度:熔覆线速度和熔覆面积率都可以表示熔覆速度。实测中物力拓高速激光熔覆线速度为20m/min-50m/min,熔覆厚度为0.2-0.6mm时,熔覆效率为0.6-1.2平方米/小时。
7、送粉方式:高速激光熔覆中的送粉器是激光熔覆质量的关键。高速激光熔覆的送粉方式主要有环形送粉和中心送粉。中心送粉比环形送粉粉末利用率高,但设计难度大,需要用圆环围住横梁。送粉管一周。目前市场上有很多圆形送粉应用。
8、保护气体压力:高速激光熔覆过程中,基体与熔覆材料之间很容易氧化,熔覆材料中含有的氧化物,会导致基体材料表面发黑、发暗、变硬,严重影响了工件表面质量。为避免熔覆材料氧化,需对工件进行保护。高速激光熔覆可在保护气体下进行,一般采用氮气或氩气作为保护气体,主要用于送粉,在激光熔覆池周围形成保护区域,减少氧化。
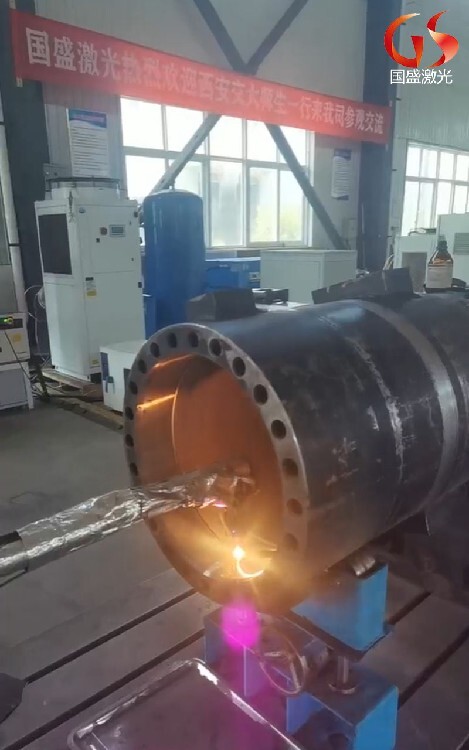
激光熔覆技术优点:
1、稀释率较低;基材上热影响区小;
2、与基体形成冶金结合,结合强度达95%以上;
3、熔覆层与基体均匀,无粗大铸造组织;
4、熔覆层及其界面结构细小,晶粒细小;
5、无空洞、夹杂裂纹等缺陷;
6、激光加工时基材表面仅轻微熔化,激光加工后不存在热变形;
7、熔覆层与基底润湿性好,结合强度高,易于实现自动化;
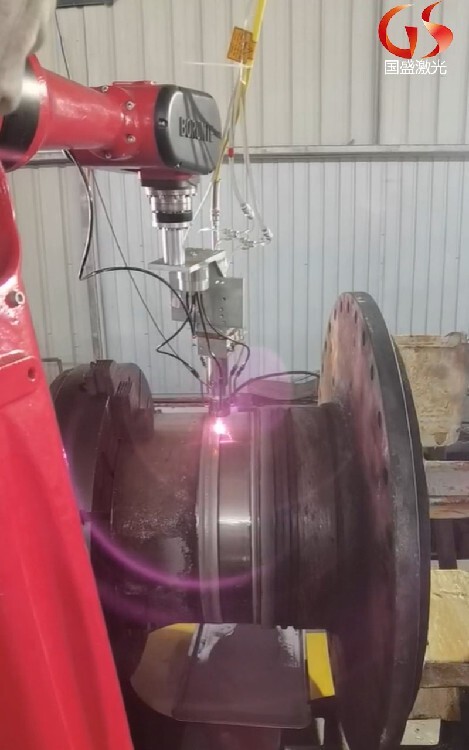
油缸内孔激光熔覆加工工艺包括以下步骤:
1、准备工件:将待加工的油缸放置在激光熔覆机的工作台上,并确保其表面清洁、无缺陷、无油渍。
2、表面处理:用砂轮或刷子等工具对气缸内孔表面进行打磨和清理,去除杂质和氧化层。
3、熔覆材料的制备:将金属粉末和合金元素按一定比例混合,加入适量的水或有机溶剂,制成熔覆材料。
4、激光熔覆加工:利用高能激光束将熔覆材料熔化并使其均匀地沉积在内孔表面。
5、后处理:对激光熔覆筒体进行热处理、研磨、抛光,提高表面硬度和光洁度。
油缸内孔激光熔覆加工的优点在于以下几个方面:
1、高硬度、耐腐蚀:通过激光熔覆技术,可以使油缸内孔表面涂层提高气缸的耐磨性和耐腐蚀性。
2、寿命长:由于激光熔覆层硬度高、耐腐蚀,可显着提高气缸的使用寿命。
3、应用范围广:激光熔覆加工可适用于各种材质、形状的气缸,可灵活应用于不同的生产环境。
4、环保节能:与传统的加工方法相比,激光熔覆加工不需要使用大量的切削液、磨料等物质,因此更加环保,降低能耗。
总之,油缸内孔激光熔覆加工是一种的加工技术,可以显着提高油缸的耐磨性、耐腐蚀性和使用寿命,并且具有环保、节能等优点。随着技术的不断发展和完善,相信这种加工技术将会在更多领域得到应用和推广。
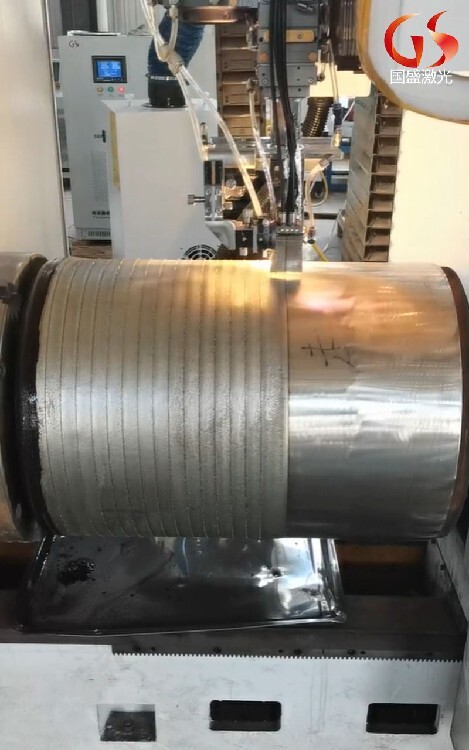
激光熔覆设备的关键配置因素
选择激光熔覆设备时,需要考虑以下关键配置因素:
1、激光功率:激光功率是激光熔覆工艺中重要的参数之一,它直接影响熔覆层的质量和效率。一般来说,激光功率越高,熔覆层的深度和宽度就越大,生产效率越高。然而,过高的激光功率可能会导致材料烧蚀和熔化过快,影响熔覆层的性能。因此,在选择激光功率时,需要根据工艺要求和材料特性进行权衡。
2、光斑尺寸:光斑尺寸是指激光束在工件表面的聚焦直径。光斑尺寸直接影响熔覆层的形状和质量。较小的光斑可实现更精细的熔覆,但也可能导致熔覆速度较慢。因此,在选择光斑尺寸时,需要根据熔覆层的精度和效率要求进行权衡。
3、扫描速度:扫描速度是指激光束在工件表面移动的速度。扫描速度越快,生产效率越高,但也可能导致熔覆层质量下降。因此,在选择扫描速度时,需要根据熔覆层的性能要求和生产效率进行权衡。
4、供粉系统:供粉系统负责将熔覆材料输送到熔覆头,熔覆过程的顺利进行。供粉系统的稳定性和准确性对熔覆层的质量有重要影响。选择供粉系统时,需要考虑其供粉能力、粉末粒度调节范围、粉末利用率等因素。
5、控制系统精度:控制系统精度是指控制系统对激光发生器、光路系统、熔覆头、工作台等部件的控制精度。控制系统的精度越高,熔覆层的成形质量和生产效率就越高。因此,在选择激光熔覆设备时,需要考虑其控制系统的精度是否满足工艺要求。
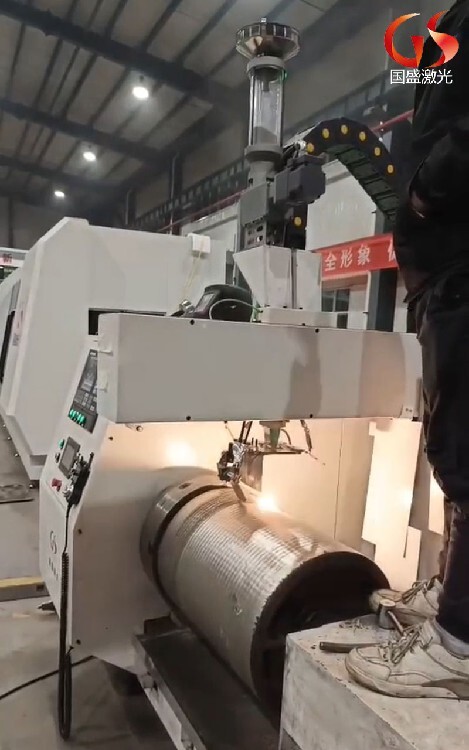
激光熔覆设备的选型策略
选择激光熔覆设备时,需要综合考虑以下几个方面:
1、明确工艺要求:明确你的工艺要求,包括熔覆材料的种类、熔覆层的厚度和宽度、熔覆速度、生产效率等要求。这些要求将直接决定所需激光熔覆设备的配置和性能。
2、比较不同品牌和型号:市场上有许多不同品牌和型号的激光熔覆设备可供选择。选择时,您可以通过比较不同品牌、型号的性能指标、用户评价、售后服务等因素,选择符合您工艺需求的设备。
3、现场检查和试用:在选择激光熔覆设备时,好对设备进行现场检查和试用。通过现场考察,了解设备的外观、结构、运行环境;通过试用设备,您可以亲身体验其操作便捷性、稳定性、熔覆效果等性能。这将帮助您更全面地了解您设备的实际情况,从而做出更明智的选择。
4、考虑成本和:在选择激光熔覆设备时,还需要考虑成本和。激光熔覆设备的价格根据品牌、型号、配置等因素而有所不同。选择时需要根据自己的预算和预期效益进行权衡,选择的设备。同时,还需要考虑设备维护成本、耗材成本、运行成本等因素,以设备长期稳定运行和盈利。
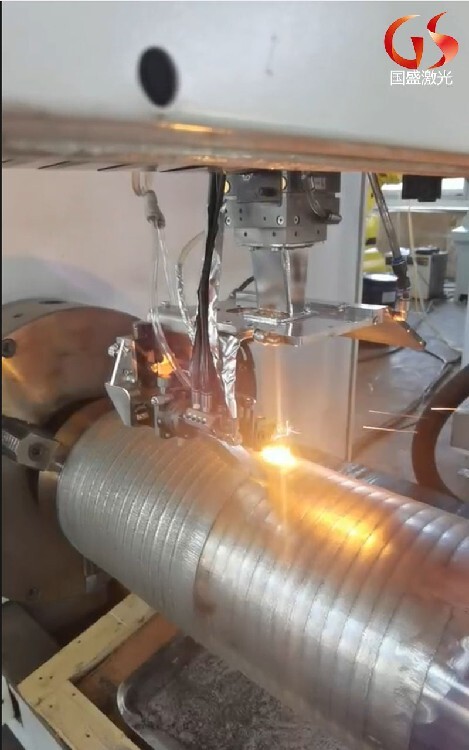
丝杆轴承位激光熔覆加工是一种、率的金属加工技术,广泛应用于各种机械制造领域。这种加工技术的主要优势在于其能够在丝杆轴承位表面形成一层坚固、耐磨、耐腐蚀的合金层,从而显著提高机械零件的使用寿命和性能。
激光熔覆加工的基本原理是利用高能激光束对金属表面进行快速加热,使其达到熔化状态,然后将预先准备好的合金粉末喷射到熔化区域,与基材实现冶金结合。通过控制激光束的功率、扫描速度和合金粉末的成分,可以在丝杆轴承位表面形成一层均匀、致密、的合金层。
与传统的机械加工方法相比,激光熔覆加工具有许多特的优势。,激光熔覆可以在不改变基材组织结构和性能的前提下,对其表面进行强化和修复,大大提高了零件的使用寿命。其次,激光熔覆加工过程中,热影响区小,变形小,能够保持零件的原始精度和尺寸稳定性。此外,激光熔覆加工还具有加工速度快、、环保等优点。
在丝杆轴承位激光熔覆加工过程中,需要严格控制各种工艺参数,如激光束的功率、扫描速度、合金粉末的成分和喷射速度等。同时,还需要对加工过程进行实时监测和调整,以确保合金层的质量和性能。此外,对于不同的材料和应用场景,需要选择适合的合金粉末和工艺参数,以达到佳的加工效果。
丝杆轴承位激光熔覆加工在机械制造领域具有广泛的应用前景。例如,在各种机械零件中,如数控机床、航空航天器、汽车发动机等,丝杆轴承位是关键的传动部件,其性能直接影响到整个机械系统的运行效率和稳定性。通过激光熔覆加工,可以在丝杆轴承位表面形成一层高硬度、高耐磨、高耐腐蚀的合金层,从而显著提高机械零件的使用寿命和性能,降低维护成本和停机时间,提高生产效率和经济效益。
此外,丝杆轴承位激光熔覆加工还可以应用于各种复杂形状和难以加工的金属零件表面。通过激光熔覆加工,可以在这些难以加工的区域形成一层的合金层,从而实现对整个零件的强化和修复。这种加工技术不仅可以提高零件的性能和寿命,还可以拓展金属零件的应用范围和适应性。
总之,丝杆轴承位激光熔覆加工是一种、率的金属加工技术,具有广泛的应用前景和重要的经济价值。随着科技的不断发展和进步,激光熔覆加工将会在更多的领域得到应用和推广,为机械制造行业的发展注入新的活力和动力。